Recognizing the Importance of Foam Control in Food and Beverage Processing
A Comprehensive Guide to Carrying Out Foam Control Solutions in Your Procedures
Efficient foam control is an important aspect of operational efficiency that frequently goes overlooked. Understanding the details of foam generation can substantially affect both efficiency and product top quality. By checking out key elements such as application compatibility and personnel training, companies can enhance their foam management initiatives.
Recognizing Foam Obstacles
Foam difficulties are a significant concern throughout different industries, affecting operational performance and product top quality. The development of extreme foam can hinder procedures such as mixing, transport, and storage, bring about increased downtime and waste. In industries like food and beverage, pharmaceuticals, and petrochemicals, foam can conflict with manufacturing lines, creating product inconsistencies and contamination risks.
In addition, foam can block devices functionality, causing pricey repair services and maintenance. For circumstances, in wastewater treatment, foam can disrupt clarifier operations, leading to reduced treatment performance and regulatory conformity problems.
Comprehending the underlying root causes of foam generation is vital for effective administration. Factors such as surfactants, temperature changes, and frustration levels can all add to foam production. Determining these components permits industries to execute targeted strategies that reduce foam development while keeping item integrity.
Types of Foam Control Solutions
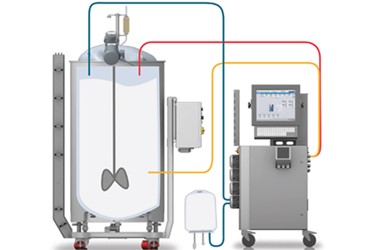
Mechanical remedies entail the use of devices such as foam skimmers or defoamers. Chemical services, on the other hand, include the application of defoaming agents-- substances that interrupt the foam framework, leading to its collapse. Foam Control.
Finally, functional techniques concentrate on process adjustments. This may involve modifying equipment parameters, such as temperature level and pressure, or transforming the circulation rates of fluids to minimize foam generation. Furthermore, carrying out great housekeeping methods can likewise mitigate foam formation by reducing contaminants that add to foam security.
Selecting the appropriate foam control remedy entails analyzing the particular demands of the procedure, including the kind of process, the features of the materials included, and safety and security considerations.
Choosing the Right Products
Picking the best foam control items requires a detailed understanding of the details application and its unique obstacles. Elements such as the sort of foam, the setting in which it occurs, and the preferred outcome all play pivotal functions in item selection. Foam Control. As an example, in industries such as food handling, it is essential to pick food-grade defoamers that conform with safety guidelines while properly managing foam.
Additionally, think about the thickness of the liquid where the foam issue exists. Some products are formulated for low-viscosity applications, while others are tailored for thicker liquids. Compatibility with existing procedures is another vital aspect; the picked foam control agents must incorporate perfectly without interrupting general procedures.
Another important variable is the method of application. Some products might need dilution, while others can be used straight. Assessing the simplicity of usage and the called for dosage can offer understandings right into the item's efficiency and cost-effectiveness.
Execution Techniques
Effective implementation strategies for foam control solutions call for a systematic approach that aligns product option with operational needs. The primary step includes a complete evaluation of the processes where foam takes place, identifying specific locations that demand treatment. By engaging cross-functional groups, consisting of quality, see this here design, and manufacturing assurance, organizations can gather understandings that educate the choice of the most reliable foam control items.
Next, it is essential to develop clear goals for foam reduction, guaranteeing that these goals are achievable and quantifiable. This may entail specifying acceptable foam levels and the timelines for execution. Training employees on the properties and application approaches of chosen foam control agents is similarly essential, as correct usage is important for optimum results.
Additionally, integrating foam control options right into existing workflows needs careful preparation. Inevitably, a well-structured technique will certainly boost operational performance while effectively handling foam-related difficulties.
Surveillance and Examining Effectiveness
Monitoring and assessing the efficiency of foam control options is essential for guaranteeing that applied strategies yield the desired results. This process involves systematic information collection and analysis to examine the efficiency of foam control representatives and techniques. Secret performance signs (KPIs) ought to be established prior to implementation, permitting a clear standard against which to determine development.
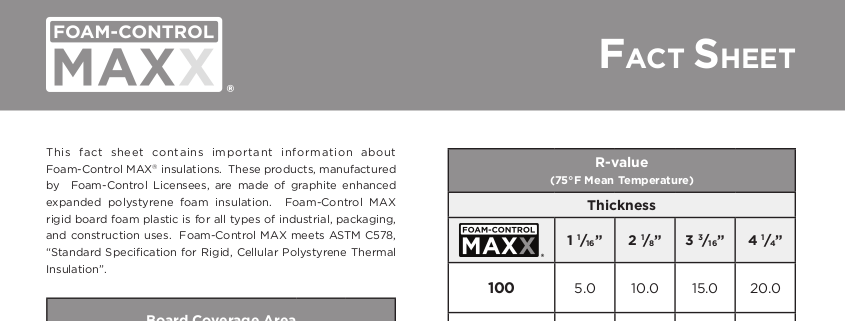
Reviewing effectiveness also requires regular testimonials of foam control treatments and representative efficiency. This can be completed via tasting and screening, permitting drivers to figure out if existing options are fulfilling operational demands. Furthermore, it is critical to solicit comments from staff member that engage with these systems daily, as their insights can reveal operational subtleties that measurable information may neglect.

Inevitably, a structured monitoring and evaluation structure aids recognize essential changes, ensuring that foam control solutions continue to be reliable, cost-effective, and lined up with organizational goals.
Final Thought
In verdict, reliable foam control options are important for maximizing operational effectiveness and keeping product quality. A thorough understanding of foam difficulties, incorporated with the choice of ideal products and application techniques, promotes the successful administration of foam generation.
Applying excellent housekeeping techniques can also minimize foam formation by minimizing impurities that contribute to foam security.
Selecting the best foam control items requires a complete understanding of the certain application and its distinct obstacles (Foam Control).Successful execution strategies for foam control services need a methodical strategy that straightens item option with functional demands.In conclusion, effective foam control services are necessary for official site optimizing operational effectiveness and preserving product high quality. A detailed understanding of foam obstacles, integrated with visit this website the option of suitable products and application approaches, helps with the effective management of foam generation